Snart kan Forsvaret printe delelageret sitt
Det norske selskapet Fieldmade vil snu opp-ned på den militære tankegangen rundt forsyning og logistikk. Korleis? Med 3D-printing og mobile mikrofabrikkar.
«Kortreist» er nøkkelordet for framtidas forsvarsmateriell. 3D-printing gjer at alle slags reservedelar kan bli produserte lokalt. For den tidlegare FFI-forskaren Christian Duun Norberg er dette starten på noko større.
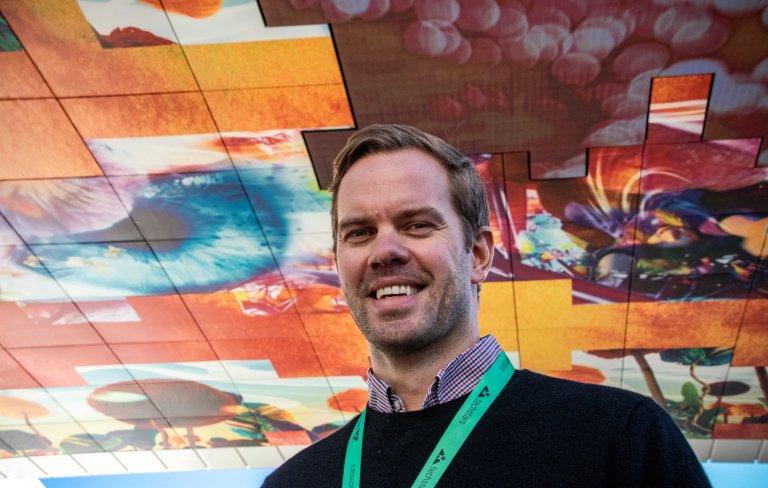
Militære toppfolk frå USA hadde stor interesse av ein spesiell personellkonteinar under Nato-øvinga Trident Juncture i 2018. På innsida av konteinaren, kalla Nomad, fekk dei sjå korleis Norbergs selskap Fieldmade produserte nøyaktige kopiar av øydelagt materiell. I toppkvalitet og på svært kort tid.
– Å få tak i ein reservedel kan ta mange dagar. Her kan ein øydelagt komponent skannast i 3D. Manglande bitar av gjenstanden blir gjenskapte. Alternativt blir komponenten produsert ut frå same datafil som originalen. Den som treng delen kan kome og hente han i døra neste dag, seier Norberg.
To gode grunnar til 3D
Det fortel Christian Duun Norberg, som er dagleg leiar i det tre år gamle selskapet. Trass i at han er berre 33 år gammal har den NTNU og NHH-utdanna Sandnes-mannen mange år bak seg i FFI og i Forsvaret – i sistnemnde mellom anna som marinejeger.
– Under Nato-øvinga demonstrerte vi dei to viktigaste grunnane til at 3D-printing er kome for å bli: Viktige komponentar kan leverast raskare, og det krevst mindre lagerhald. Hugs: Eit fysisk lager krev både plass og lokalisering, kanskje langt unna dei som har behov for leveransen. Eit digitalt lager krev ingen av delane.
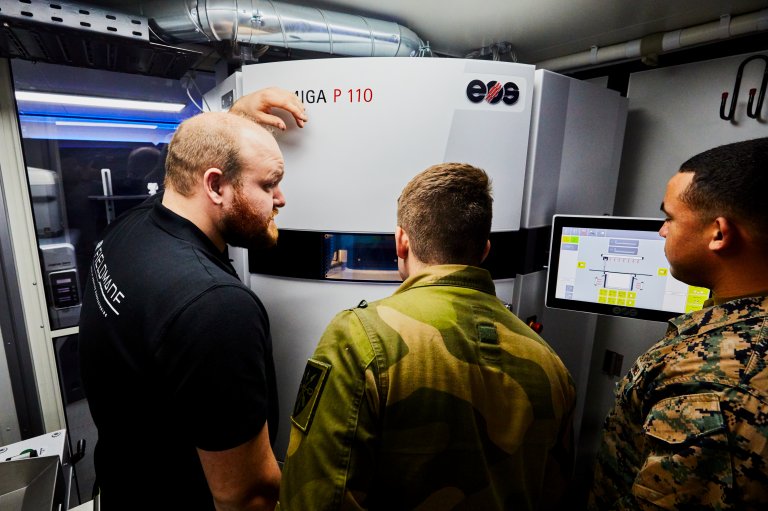
Det førebels fem personar store firmaet er pionerar innanfor 3D-trykte reservedelar. Men dei tenker ikkje på seg sjølve som ein mikrofabrikk. Visjonen er større enn som så. Fieldmade er ein tidleg representant for det som blir kalla tilsettingsindustri, på engelsk additive manufacturing (AM).
Slik industri vil ha en enorm innverknad på den militære forsyningskjeda og korleis den blir styrt. Dette er nær framtid, seier Christian Duun Norberg. Så langt har ikkje godt utvikla tilsettingsfabrikker, med vekt på forsvar, vore i marknaden. Men no har snøballen byrja å rulle.
Forsvaret er ikkje åleine om å sjå behovet for kortreist produksjon av vitale delar.
Handplukka til rask utvikling
Vi møter Christian Duun Norberg i Equinors hovudkontor på Fornebu. Fieldmade er eitt av tre norske selskap som dette halvåret har plass i Techstars Energy. Dette er ein såkalla akselerator. Handplukka selskap får støtte og finansiering som gjer dei i stand til å utvikle seg fortare. Med på Techstar-laget er også Kongsberg-gruppa og Capgemini.
– For oljebransjen er det avgjerande med løysingar som aukar driftsevna og beredskapsnivået. Vi kan tilby produksjonslaboratorier på staden. Vi er i stand til å digitalisere kundanes reservedelslager, rett og slett. I forlenginga av det kan vi slutte å snakke om «reservedelar». Det nye delelageret har du på sett og vis i lomma, same kvar du er.
Langt meir enn boksen
Mobiliteten til Nomad-konteinaren er viktig for Forsvaret.
– Men det sentrale for oss er ikkje å lage boksar. Målet er større enn som så. Fieldmade arbeider enkelt sagt med å systematisere det digitale økosystemet. Vi er ei verksemd som arbeider for å endre ein tankegang om store varelager og gammaldags logistikk. Fellesnemnaren er lik for Forsvaret og Equinor. I Equinors tilfelle vil konteinarane mellom anna kunne brukast som 3D-verkstader på plattformene i Nordsjøen. Slik vil ein minske behova for kostbar lagring på land, og transport ut.
Fieldmade blei til hos FFI på Kjeller. Forskarane Joakim Flathagen og Harald Hovland var blant eldsjelene som bidrog med prosjektsøknaden til Forskingsrådet. I denne fasen blei namnet Fieldmade foreslått – eit namn som nokså presist fortel kva dette dreier seg om. Prototypeverkstaden ved FFI var også sentral. Christian Duun Norberg har rekruttert Kristin Wille von der Lippe herifrå. Ho jobba tidlegare på FFIs prototypeverkstad og var med i prosjektet frå instituttets side.
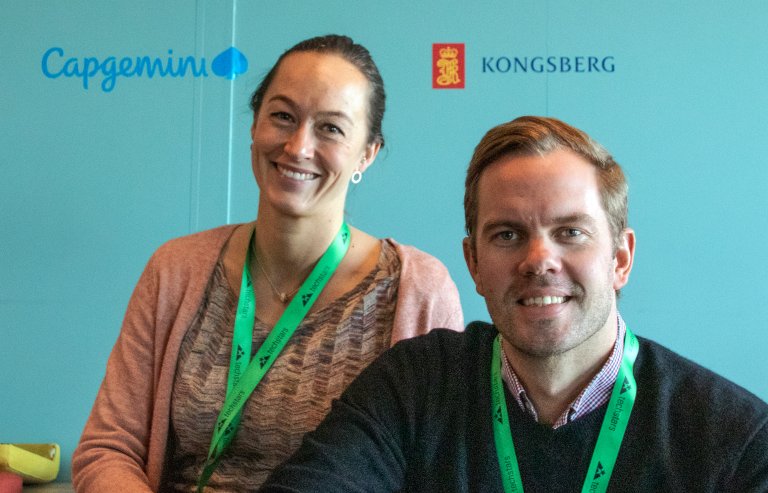
Ein knopp frå FFI
Dette er den typen knoppskyting som FFI ønsker.
– Det var avgjerande å få arbeide der. På FFI fann eg folk med sams interesser. Dermed blei det ein spanande stad å jobbe. Vi var ein dugnadsgjeng på tre-fire personar, som gjorde dette ved sida av det prosjektet vi eigentleg heldt på med. På sett og vis utdanna vi oss sjølve. Ut av dette materialiserte det seg noko som elles berre ville forblitt ein god idé. Brått var vi blitt sju, og dermed gjekk ideen over til å bli eit eige prosjekt, seier Norberg.
Totalt er det til no investert 30 millionar i Fieldmade, ein liten sum når ein tenker på potensialet.
Topp konteinar-design
Så langt har Fieldmade utvikla tre konteinarar: Nomad 1, 2 og 3. Ein har vore i aktiv bruk på Sessvollmoen, og skal no vidare til Bergen. Ein fjerde konteinar er på teiknebrettet.
Eker Design har vore med og utvikla sjølve konteinaren. Ikkje berre er den lekker å sjå til – noko som aukar appellen overfor alle nysgjerrige – den er også funksjonell.
– Eker var dyktig til å tenke på korleis løysinga skulle fungere godt i praksis. Dei fekk det til. Løysningane Fieldmade utviklar reduserer også behovet for høg spesialisering. To soldatar kan med litt opplæring handtere produksjonen frå det digitale varelageret i felt, og oppdukkande problema kan prosesserast heime. Difor er systema i aktiv bruk i Forsvaret allereie.
Norberg seier at han opplever ei auka interesse for noko som ikkje tidlegare blei så godt forstått.
– Mange ser fordelane. Vi snakkar om auka operativ evne, nedbygging av delelager og altså ein økonomisk gevinst som kan bli temmeleg stor. For kvifor skal Forsvaret ha hundrevis av komponentar på lager når 3D-printing kan generere dei ti som trengst i morgon? Utfordringa er å få eksisterande organisasjonar til å tenke i denne retninga. Det er ikkje teknologien det står på, men prosessane rundt.
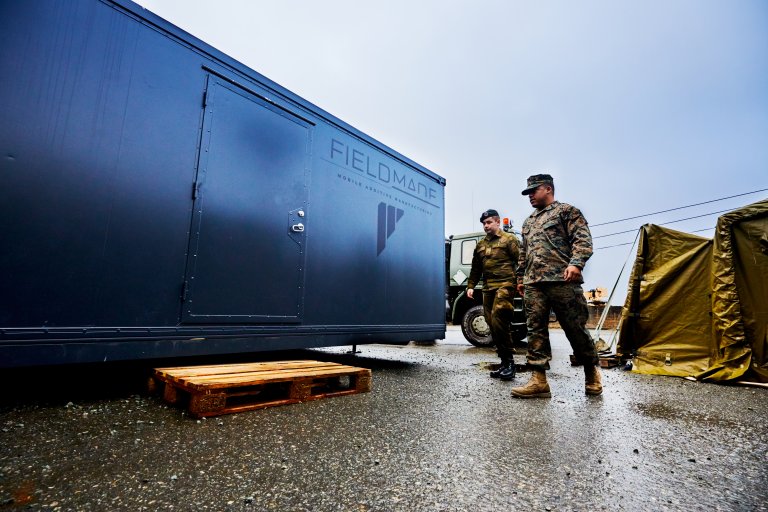
Alt kan lagast
Framstillinga av ein reservedel med 3D-printing kan ta frå timar til eit døgn eller to, avhengig av storleik og material. Teknisk kan ein nytte polymerar, eller ulike metall som aluminium, titan og rustfritt stål. Det er også enkelt å lage mjuke delar, til dømes pakningar.
Produkta herifrå blir like gode som frå ein tradisjonell fabrikk; kvaliteten er identisk. Christian Duun Norbergs visjon er at mikrofabrikkane med blir så bra at dei gjer stort lagerhald av mange ting overflødig.
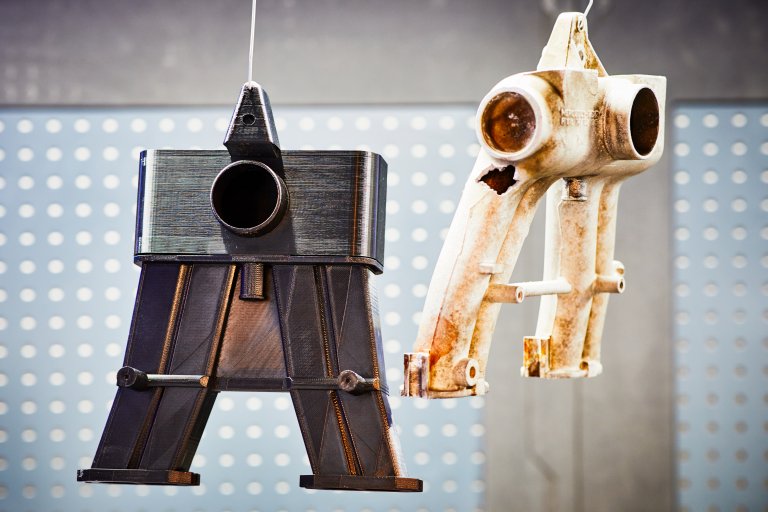
– Vi snakkar mindre og mindre om dette som reservedelar. Vi kan kutte i delelager og likevel få betre beredskap. Hugs dessutan at det ikkje er noko nytt at Forsvaret sjølv produserer mange av dei tinga dei treng. Dette er høgverdig industri, som no blir flytta nærare brukarane.
No jobbar han med å skape ein digital marknadsplass for 3D-produksjon av delar, retta mot militære behov.
– Eg opplever ei auka interesse for noko som ikkje tidlegare blei så godt forstått. Verda treng å modnast. Forsvaret må sjå potensialet. Forsvarsindustrien tener godt på dei løysingane som finst i dag. No må vi samarbeide om å kome vidare.
Mars neste?
Christian Duun Norberg er fødd og oppvaksen i Sandnes. Om nokon lurer på Christian Duun Norberg-namnet: Ja, han er i slekt med den kjente forfattaren Olav Duun.
Likskapen mellom forfattar Duun og gründer Duun Norberg er kanskje at berre fantasien set grenser:
– 3D er eit heitt tema i Nato. I mange av medlemslanda arbeider dei med dette. Men Fieldmade står ikkje tilbake for andre prosjekt. Under øvinga samarbeidde vi med US Marine Corps. Vi framstilte delar som dei ikkje klarte. Det blei trekt fram av militærtoppane som var på besøk. Moralen er: Dette kan vi få til i vesle Noreg. På den andre sida ligg amerikanarane langt framme i det som er eit neste tenkbare steg for denne typen teknologi. Made in Space er ei amerikansk verksemd som ser for seg at 3D-printing på Mars, med lokale material og ressursar, kan gi grunnlag for busetnad der. Det er ekstremversjonen. Den er likevel innanfor rekkevidde, teknologisk sett.